Compression springs are integral components that facilitate reliable operation of your punch stripper assembly system. Every spring requires a precisely tuned spring rate in order to exhibit the specific compression and rebound properties needed to achieve accurate and repeatable punch press operations.
Whether your equipment utilizes conventional steel compression springs or high-performance polyurethane compression springs, the springs themselves tend to wear out after extended use in the factory. Replacing worn compression springs as soon as you notice any sign of issues is crucial to avoid spring failure, forced downtime, or just general performance degradation which can impact the quality of your stamped products.

for Manufacturing Facilities and Warehouses
Polyurethane Products manufactures a complete range of custom storage options
to efficiently handle your sheet metal rolls and other material coils.
A Closer Look at Punch Stripper Compression Springs:
The main function of a punch stripper spring is to absorb shock as the press punches in and out of the metal, thus providing stability to minimize manufacturing errors and distortion. As the punch withdraws, the stripper spring helps the workpiece “pop” cleanly free from the press tooling. As a result, punch press operations are more reliable and consistent, while the risk of damage to the equipment or workpiece is minimized.
Troubleshooting Punch Press Compression Springs:
- Punch stripping errors such as stuck parts or rough edges are often by overly worn or damaged springs. Essentially, the spring material fatigues to a point that its resistance compressive and rebound forces is compromised.
- Malfunctioning punch stripper compression springs will commonly produce puckered holes with raised edges. This puckering effect is due to the punch tooling essentially “sticking” to the workpiece metal as it is withdrawn.
- Every punch stripper spring must maintain close to the exact specified spring rate at preload. This pressure is carefully calculated by considering the pressure required in relation to the spring travel. As the springs become overly worn, testing may reveal inconsistent spring rates at the desired preload set point.
- Compressing punch stripper springs past the maximum suggested operating range can severely impact performance or irreversibly damage the spring. Pushing the material past its intended travel can permanently deform the spring, necessitating immediate replacement.
The Result of an Underperforming Punch Stripper System:
Worn-out compression springs can lead to punch stripper malfunctions or total spring failure. If that happens, the resulting equipment damage and downtime can far outweigh the cost of initial replacement of the springs. Furthermore, as the springs lose their ability to properly absorb residual pressure, you may end up damaging other components within the punch press equipment . This is why proper spring selection, maintenance, and replacement are critical.
Quality American Manufactured Punch Stripper Springs and Other Industrial Products
Polyurethane Products is a leading American manufacturer of punch stripper compression springs and other quality industrial components. Our urethane punch strippers and compression springs are utilized by stamping operations across the nation to achieve better equipment efficiency, reliability, and performance.
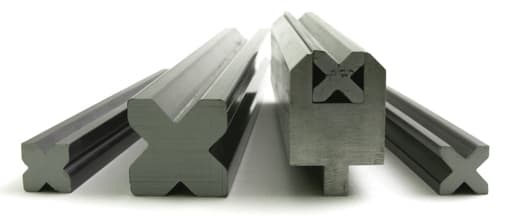
You have questions, we have answers. Contact us today. Our skilled customer service specialists can help you make the right choice in polyurethane applications.